Pad Printing Technology & Innovation
TouchMark has worked closely with leading medical device manufacturers, R&D and Design Engineers, during both prototype and production phases, to develop pad printing processes that meet their specific needs including:
- Surface Pre and Post Treatment
- Micro-Vu Inspection
- Ink Selection for Maximum Adhesion
- Curing
- Catheter, Microcatheter Printing
- Print Durability Testing
- Specialty Inks
Medical Pad printing offers many advantages over other forms of marking and labeling, especially in the invasive medical device and diagnostic world. The ability to cost-effectively handle anything from small parts with microscopic printing to large panels while maintaining superior quality is one of the TouchMark advantages. Medical device pad printing on difficult or irregular surfaces is also one of TouchMark's specialties. Whether it’s a 360° rotational catheter, microcatheter or a USB connector print. TouchMark has the expertise to pad print on virtually any surface.
TouchMark has developed proprietary processes to pad print on difficult substrates including:
- Silicone
- FEP
- Nitinol
- PEEK
- PTFE
- PEBAX
- Delrin
Cleanroom Manufacturing Facility and ISO 9001:2018 Certified Standards:
TouchMark’s state-of-the-art cleanroom production facility assures that your pad printing projects will be produced in a controlled environment where quality is constantly monitored. In accordance with ISO requirements, TouchMark maintains quality systems throughout the medical device pad printing process to ensure consistency of handling, lot control integrity, product traceability, and quality system maintenance.
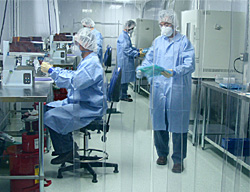
ISO 9001:2008 Cleanroom Facility
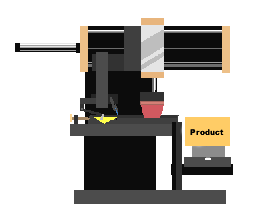